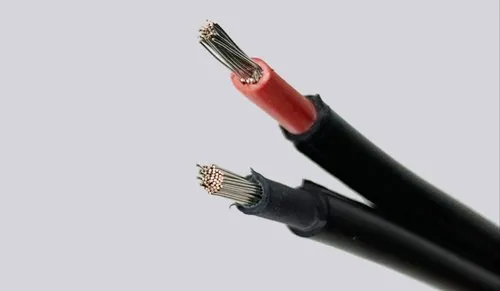
Currently, the commonly used insulation material for DC cables is polyethylene. However, researchers are continuously seeking more potential insulation materials, such as polypropylene (PP). Nonetheless, using PP as a cable insulation material presents several problems.
1. Mechanical Properties
To meet the basic requirements for the transportation, installation, and operation of DC cables, the insulation material must possess certain mechanical strength, including good flexibility, elongation at break, and low-temperature impact resistance. However, PP, as a highly crystalline polymer, exhibits rigidity within its working temperature range. Additionally, it shows brittleness and susceptibility to cracking in low-temperature environments, failing to meet these conditions. Therefore, research must focus on toughening and modifying PP to address these issues.
2. Aging Resistance
During long-term use, DC cable insulation gradually ages due to the combined effects of high electric field intensity and thermal cycling. This aging leads to a reduction in the mechanical and insulation properties, as well as a decrease in breakdown strength, ultimately affecting the reliability and service life of the cable. Cable insulation aging includes mechanical, electrical, thermal, and chemical aspects, with electrical and thermal aging being the most concerning. Although adding antioxidants can improve PP's resistance to thermal oxidative aging to a certain extent, poor compatibility between antioxidants and PP, migration, and their impurity as additives affect PP's insulation performance. Therefore, solely relying on antioxidants to improve PP's aging resistance cannot meet the lifespan and reliability requirements of DC cable insulation, necessitating further research on modifying PP.
3. Insulation Performance
Space charge, as one of the factors influencing the quality and lifespan of high-voltage DC cables, significantly impacts the local electric field distribution, dielectric strength, and insulation material aging. Insulation materials for DC cables need to suppress the accumulation of space charge, reduce the injection of like-polarity space charges, and hinder the generation of unlike-polarity space charges to prevent electrical field distortion within the insulation and interfaces, ensuring unaffected breakdown strength and cable lifespan.
When DC cables remain in a unipolar electric field for an extended period, the electrons, ions, and impurity ionization generated at the electrode material within the insulation become space charges. These charges rapidly migrate and accumulate into charge packets, known as the accumulation of space charge. Therefore, when using PP in DC cables, modifications are necessary to suppress charge generation and accumulation.
4. Thermal Conductivity
Due to poor thermal conductivity, heat generated during the operation of PP-based DC cables cannot dissipate promptly, resulting in temperature differences between the inner and outer sides of the insulation layer, creating an uneven temperature field. The electrical conductivity of polymer materials increases with rising temperatures. Therefore, the outer side of the insulation layer with lower conductivity becomes prone to charge accumulation, leading to reduced electric field intensity. Moreover, temperature gradients cause the injection and migration of a large number of space charges, further distorting the electric field. The greater the temperature gradient, the more space charge accumulation occurs, intensifying the electric field distortion. As discussed earlier, high temperature, space charge accumulation, and electric field distortion affect the normal operation and service life of DC cables. Hence, improving the thermal conductivity of PP is necessary to ensure the safe operation and prolonged service life of DC cables.
Post time: Jan-04-2024