Submarine cables play a vital role in global communications, carrying vast amounts of data across oceans. Selecting the right materials for these cables is crucial to ensure their durability, performance, and reliability in challenging underwater environments. In this article, we will explore the challenges involved in choosing materials for submarine cables and discuss the solutions that can help in making informed decisions.
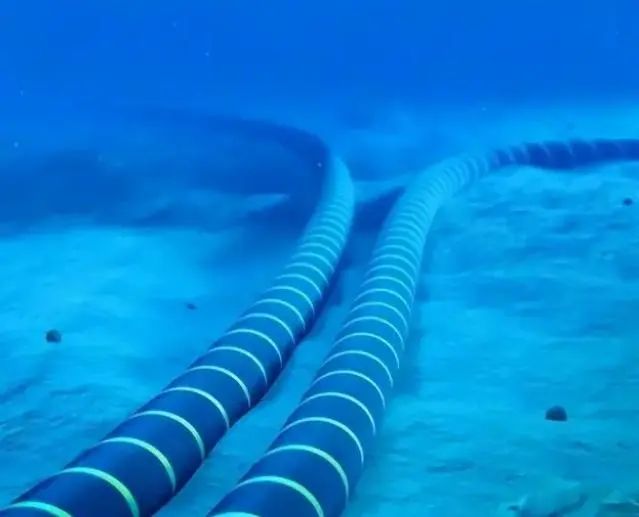
Corrosion Resistance:
One of the primary challenges in submarine cable design is corrosion. The cables are exposed to seawater, which can cause significant corrosion damage over time. Selecting materials with excellent corrosion resistance is essential for prolonged cable life. Solutions such as using corrosion-resistant alloys like stainless steel or utilizing specialized coatings can provide effective protection against corrosion.
Mechanical Strength:
Submarine cables need to withstand immense pressure and mechanical stress due to ocean currents, tides, and the weight of water. Choosing Materials for Submarine Cables with high mechanical strength is crucial to ensure the cables can withstand these forces without compromising their integrity. High-tensile strength materials like aramid fibers and carbon fiber-reinforced polymers (CFRP) are commonly used to enhance the mechanical properties of submarine cables.
Water Blocking and Insulation:
Maintaining proper insulation and water-blocking properties is vital to prevent water ingress and protect the cable’s internal components. Polyethylene, polypropylene, and cross-linked polyethylene (XLPE) are commonly used for insulation and water-blocking layers in submarine cables. These materials offer excellent electrical insulation properties and can resist the penetration of water, ensuring optimal cable performance and longevity.
Flexibility and Bend Radius:
Submarine cables often need to be flexible and capable of withstanding repeated bending without compromising their performance. Materials for Submarine Cables with high flexibility and low bending stiffness, such as certain types of polyurethane and elastomers, are commonly used to ensure the cables can be installed and maintained in various underwater conditions while maintaining their electrical and mechanical integrity.
Thermal Stability:
Submarine cables may experience significant temperature variations in underwater environments. It is crucial to select Materials for Submarine Cables with excellent thermal stability to ensure the cables can withstand these temperature changes without affecting their performance. Thermoplastic materials like polyethylene and polypropylene offer good thermal stability, making them suitable choices for insulation and sheathing layers.
Conclusion:
Choosing the right materials for submarine cables is a critical process that involves considering challenges specific to underwater environments. By addressing factors such as corrosion resistance, mechanical strength, water blocking, flexibility, and thermal stability, cable manufacturers and operators can ensure the optimal performance and longevity of submarine cables. Understanding these challenges and implementing appropriate material solutions is essential for reliable and efficient global communication networks.
Post time: May-02-2023